The newly renovated Kline Chemistry Laboratory features bright, open work spaces and shiny new lab benches, and now, high performance fume hoods raise the bar for user safety and energy efficiency. More than 60 high efficiency fume hoods have been installed at KCL, representing Yale’s first large-scale deployment of this style of fume hood which are 30% more efficient than traditional fume hoods.
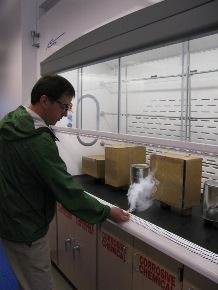
In research laboratories, fume hoods enable users to safely handle hazardous chemicals while fumes are expelled out of the building. The operation of fume hoods also requires a significant amount of energy. The air that flows through a fume hood is drawn from the air in the room which is conditioned (heated/cooled) by the building’s ventilation system. The more air that is taken in by the fume hoods, the greater the ventilation and energy demands.
The new high efficiency fume hoods in KCL are more aerodynamic than traditional fume hoods, with smoother edges and a better design. These hoods are being operated with a face velocity of 80 feet per minute (face velocity indicates the speed at which the air enters the fume hood chamber). Sensors detect when the fume hoods are in use; the face velocity is set back to 60 feet per minute when not in use. In comparison, most fume hoods at Yale operate with a face velocity of 100 feet per minute, while older models were operated at 150 feet per minute or more.
A common misperception exists that higher face velocities are always safer, but in fact, face velocities over 150 feet per minute can create eddies and turbulence in the air, which can cause chemical fumes to spill out from the hood. The new hoods require approximately 30% less air intake than traditional fume hoods and are also extremely safe.
By requiring less air intake, laboratory ventilation systems can be sized more appropriately and run more efficiently, reducing both capital and operating costs. The operation of a single fume hood at 100 ft/min costs on average $3500-$4500 per year in energy costs, which means that each new high efficiency fume hood will save Yale approximately $1000/year in energy costs. In KCL, this amounts to approximately $50,000 of energy savings per year.
For this installation, Yale Environmental Health and Safety as well as Facilities Operations have required that the new fume hoods must pass the ASHRAE[1] 110 laboratory fume hood performance test, following a defined method of evaluating the fume hood’s ability to contain and exhaust fumes under a set of standard conditions. The new fume hoods for KCL were commissioned in March and April 2014 by Safety Plus, LLC, an independent third party vendor. Every single fume hood in KCL was individually tested and all were determined to be performing properly.
The ASHRAE 110 test is comprised of three parts, which take approximately 30 minutes to complete per fume hood: first, a device measures the air inflow (face) velocity; second, a visual smoke test is conducted with a smoke emitter to see how the air is moving inside the fume hood; and third, a tracer gas is introduced into the hood and a machine attached to a mannequin detects whether any gas escapes from the hood over a 15 minute period to determine whether a person would breathe in chemical fumes while working at the hood.
Yale has approximately 1200 fume hoods across campus. Other laboratories at Yale such as in the Chemistry Research Building (CRB) have standard fume hoods with variable air volume controls (VAV), in which the volume of air changes depending on the height of the sash opening, reducing unnecessary air intake. But the newest high efficiency fume hoods installed in KCL utilize VAV controls on high efficiency hoods, and are therefore even more efficient and save more energy than the standard VAV hoods.
“We and our colleagues in Facilities / Systems Engineering worked very hard and creatively with the design team and the intended occupants to develop innovative approaches for the new KCL. These included computerized fluid dynamics modeling to optimize the supply and exhaust ventilation systems, and a detailed selection process of commercially-available high performance fume hoods. We are very excited to finally see the labs being occupied and put to use,” said Rob Klein, Deputy Director of Yale Environmental Health and Safety.
[1] ASHRAE was formed in 1984 as the American Society of Heating, Refrigerating and Air-Conditioning Engineers