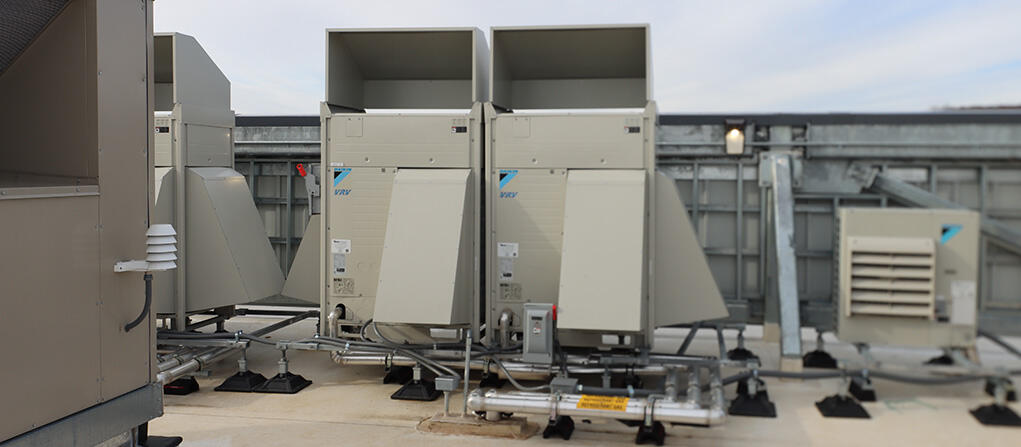
It used to be that Yale Facilities staff would find out about malfunctioning mechanical equipment only after getting a massive energy bill. By that time—often weeks after the issue occurred—energy and money were already wasted and the process to review every unit in a building to find the root cause was a daunting task.
A newer technology that uses fault detection algorithms and predictive logic is now helping Yale pinpoint these mechanical faults in real-time—saving energy and money, and moving the university closer to its goal of being a net-zero emissions campus by 2035.
The analytics software, referred to as automatic fault detection and diagnostics (AFDD), processes data from building mechanical systems and energy meters to find problems and identify the root causes, while evaluating the performance of building systems for energy, comfort, and maintenance.
Yale has used building automation systems since the mid-1980s to program the thousands of air handling units and other pieces of equipment that serve the campus. These building automation systems are good at controlling machines to turn on and off, to respond to set points for temperature and humidity, and to alert staff when equipment has failed. However, there are common malfunctions that a building occupant might never notice—and which would not trigger an alert.
A common example is an air-handling unit that simultaneously heats and cools fresh intake air because of faulty valves. It won’t impact comfort in the building—or trigger an alert—because the competing heating and cooling effectively cancel each other out and the building temperature remains constant. A staff member could find the issue if they happened to go looking for it, but monitoring hundreds of units around the clock with limited staff simply is not possible.
Enter AFDD. The analytics software, adopted by Yale in 2019, can analyze thousands of data points within mechanical systems across the campus and report problems as they happen. Using algorithms and predictive logic, the software can take in information from Yale building systems and energy meters and make judgment calls about whether the systems are performing well. Crucially, it also projects the cost—in both energy and dollars—of not fixing a malfunction, helping Yale’s energy analysts to prioritize the most urgent repairs.
“The university invests considerably in energy-efficient mechanical systems for high performance buildings,” says Ed Lipsett, a senior mechanical engineer in the Office of Facilities. “Using this software allows us to keep these systems in good working condition. It is very important.”
A Key to Unlocking Yale’s Climate Targets
Energy conservation is a key pillar of Yale’s approach to becoming a net-zero emissions campus by 2035 and to produce zero actual emissions by 2050. To meet those ambitious targets, the university forecasts it will need to reduce energy use by nearly half over the next two to three decades, even as we grow the campus each year.
The analytics software advances that goal by allowing staff to identify and quickly repair malfunctioning energy systems and to maintain the performance of building equipment and systems, something known as “energy persistence.”
“A really important aspect of our long-term plan is to sustain the savings that we’ve earned,” explains Julie Paquette, Yale’s Director of Engineering and Energy Management. “Systems degrade over time. So, if you’ve made a real investment in a building or system and you’re expecting a certain level of performance, you need to maintain that. This technology helps us to do that.”
Along with energy savings, the software is also delivering significant financial benefits.
During fiscal year 2022, AFDD was deployed on more than 650 air handling units across campus, leading to a savings of $580,000 in direct energy costs. The energy saved in that time was 17,700 MMBTU, or roughly the amount used by 250 average Connecticut households annually.
From the analytics website, Paquette’s energy team can see a dashboard listing every piece of mechanical equipment on campus that is reporting a problem. When they get an alert, they hop onto another interface—a building automation system platform—to investigate the reported problem and assign a work order to repair it, based on priority.
“If we had dozens of people to look at these systems, we wouldn’t need the analytics software,” says Steven Unger, an energy systems analyst in the Office of Facilities. “But we don’t have that ability. Analytics is able to look for problems 24/7.”
A Better Way to Onboard New Buildings
The analytics software has also been helpful in uncovering problems during the process known as “building commissioning.” Newly opened or renovated buildings come with a one-year warranty period, during which time the project team is responsible for addressing any uncovered problems with building performance.
The previous way of searching for problems during this period was a “snapshot in time” approach—running functional performance tests on individual pieces of equipment at static points in time. That method is prone to missing any problems that are not occurring when those snapshots are taken, explains Lipsett. With analytics, Lipsett says, Yale can now run diagnostics 24/7 for a full year on new building mechanical systems, testing them through every season and occupancy level while assuming responsibility for their upkeep.
This approach was piloted for the first time at Yale on the Schwarzman Center when it opened in 2021. Analytics helped find twice as many issues as conventional approaches to commissioning—many of which might have otherwise gone unnoticed.
“We are really excited about the future of commissioning with tools like AFDD software and about its potential to help Yale achieve its broader climate action,” says Paquette.